How to Glaze Air Dry Clay: Complete Guide for Beautiful Results
Air dry clay has become incredibly popular for crafting because it doesn’t require a kiln. However, many crafters struggle with achieving that professional, glazed finish that makes pottery shine.
While traditional pottery glazes require high-temperature firing, you can still create beautiful glazed effects on air dry clay using alternative methods.
In this guide, I will walk you through everything you need to know about glazing air dry clay projects to achieve professional-looking results.
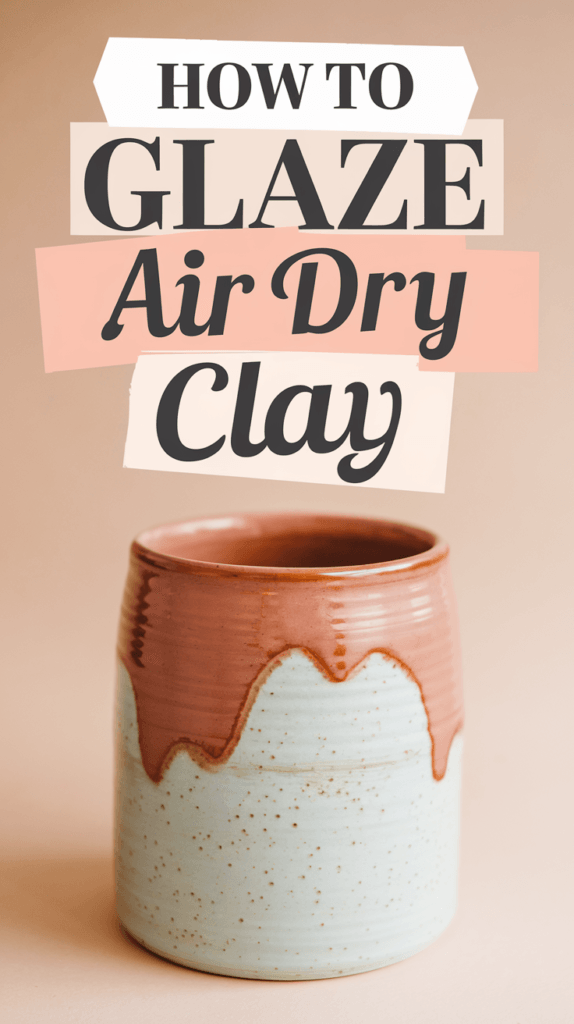
What You Need to Glaze Air Dry Clay
Before starting the glazing process, gather these essential materials:
- Air dry clay project (completely dried for at least 72 hours)
- Varnish or sealant (clear nail polish, acrylic gloss medium, or commercial varnishes)
- Foam brush or paintbrush for smooth application
- Acrylic paint (optional, for adding color to your glaze)
- Non-porous work surface (tile, glass, or plastic sheet)
- Fine-grit sandpaper (optional, for smoothing surfaces)
- Clean cloth for wiping away dust
- Small container for mixing custom glazes
The type of varnish you choose will significantly impact your final results. Commercial options like DecoArt Triple Thick Glaze create excellent glossy finishes, while acrylic mediums offer more versatility for customization.
Preparing Your Air Dry Clay for Glazing
Proper preparation is crucial for successful glazing. Follow these important steps:
Ensure Complete Drying
Your air dry clay must be completely dry before applying any glaze or varnish. Depending on the size and thickness of your piece, this typically takes at least 72 hours. For thicker pieces, allow up to a week of drying time.
Test for dryness by gently pressing on the thickest part of your project. If it feels cool or yields to pressure, it needs more drying time.
Smooth Surface Preparation
For the most professional finish, consider these preparation steps:
- Lightly sand any rough areas using fine-grit sandpaper
- Wipe away all dust with a slightly damp cloth
- Allow the piece to dry completely after wiping
- Inspect for any cracks or imperfections that need repair
Sealing Porous Clay (Optional)
Air dry clay is naturally porous, which can affect how varnish adheres. For the best results, consider applying a thin layer of PVA glue diluted with water (1:1 ratio) as a primer before glazing. This creates a sealed surface that accepts varnish more evenly.
Creating DIY Glazes for Air Dry Clay

While commercial varnishes work well, you can create custom DIY glazes that mimic traditional ceramic glazes.
Basic Clear Glaze Recipe
For a simple clear glaze that creates a shiny finish:
- Mix 2 tablespoons clear craft glue
- Add 3 tablespoons water
- Add 1 bottle of clear nail polish
- Stir gently to avoid creating bubbles
Colored Glaze Recipe
To create colored glazes that mimic traditional pottery glazes:
- Start with the basic clear glaze recipe above
- Add small amounts of acrylic paint gradually
- Test the color on a scrap piece of dried clay
- Adjust color intensity by adding more paint as needed
This approach gives you complete control over the color and opacity of your glaze.
Step-by-Step Glazing Process

Follow this detailed process for the best glazed finish on your air dry clay:
1. Prepare Your Workspace
Place your clay piece on a non-porous surface like glass, tile, or plastic. This prevents your project from sticking during the glazing process. Ensure good ventilation, especially when using commercial varnishes.
2. Apply the First Layer
Using a foam brush provides the smoothest application:
- Dip your brush into the varnish or DIY glaze
- Apply a thin, even layer using long, smooth strokes
- Work in one direction to minimize brush marks
- Ensure complete coverage but avoid excess pooling
The first layer primarily seals the surface and provides a foundation for building gloss depth.
3. Allow Proper Drying Time
Patience is essential for quality results:
- Let the first layer dry completely (5-6 hours minimum)
- Avoid touching the surface during drying
- Keep away from dust and lint
- Ensure the piece is in a warm, dry environment to accelerate drying
4. Apply Additional Layers
Building up layers creates that beautiful deep glazed look:
- Apply a second layer using the same technique as the first
- Cross-stroke application (perpendicular to the first layer) helps eliminate brush marks
- Allow complete drying between each layer
- Continue adding layers until you achieve your desired finish
Most projects require 3-5 layers for a professional glazed appearance.
5. Final Finishing
After your final layer has dried completely:
- Inspect the piece in good lighting for any missed spots
- Apply touch-ups as needed
- Allow at least 24 hours of curing time before handling regularly
- Keep glazed pieces away from excessive heat or moisture
Comparing Glazing Options for Air Dry Clay
Different varnishes and sealants produce different effects. This comparison helps you choose the right option for your project:
Glaze Type | Finish | Durability | Drying Time | Best For |
---|---|---|---|---|
Acrylic Gloss Medium | Medium shine | Good | 1-2 hours | Most projects |
Mod Podge Gloss | Subtle shine | Moderate | 15-20 minutes | Beginner projects |
Triple Thick Glaze | High gloss | Excellent | 24 hours | Display pieces |
DIY Clear Glaze | Customizable | Varies | 5-6 hours | Experimental work |
Nail Polish | Ultra glossy | Good | 10-15 minutes | Small details |
Advanced Glazing Techniques
Once you master basic glazing, try these advanced techniques for spectacular effects:
Creating Crackle Effects
The crackle glaze effect mimics antique pottery:
- Apply a base layer of white or cream acrylic paint
- Let dry completely
- Apply a thick layer of PVA glue
- Let it partially dry until tacky
- Apply a contrasting color of thinned acrylic paint over the glue
- As everything dries, cracks will form naturally
Ombre Glazing
Create beautiful gradient effects with this technique:
- Prepare two different colored glazes
- Apply one color at one end of your piece
- Apply the second color at the opposite end
- While both are still wet, blend gently where they meet
- Allow to dry completely before adding additional layers
Textured Glazing
Textured finishes add depth and visual interest:
- Apply a base layer of glaze and let dry
- Mix fine materials (sand, coffee grounds, or baking soda) into your glaze
- Apply this textured mixture in patterns or all over
- Seal with a final clear layer of glaze
Common Glazing Problems and Solutions
Even experienced crafters encounter issues. Here’s how to solve common problems:
Sticky Finish
If your glazed piece remains tacky after drying:
- You applied layers too thickly
- Solution: Wipe off excess with a cloth dampened with rubbing alcohol and apply thinner layers
Bubbles in Glaze
Bubbles ruin a smooth finish:
- Caused by shaking the varnish or applying too quickly
- Solution: Gently pop bubbles with a toothpick while still wet
Uneven Glossiness
Some areas shine while others appear dull:
- Inconsistent application or porous surface issues
- Solution: Apply an additional thin layer focusing on dull areas
Caring for Glazed Air Dry Clay Projects
Proper care extends the life of your glazed clay pieces:
- Dust regularly using a soft brush or cloth
- Avoid water exposure as prolonged moisture can damage air dry clay
- Display away from direct sunlight to prevent color fading
- Handle with clean hands to prevent oils from affecting the finish
- Reapply a thin glaze layer annually for pieces you want to preserve long-term
Remember that while glazed air dry clay looks similar to kiln-fired ceramics, it isn’t waterproof or food-safe. Never use these pieces for food or beverages.
Final Thoughts
Mastering how to glaze air dry clay opens endless creative possibilities without needing expensive equipment. With the right materials and techniques, your air dry clay creations can achieve beautiful, professional-looking finishes that rival traditional ceramics.
Remember that each layer builds both protection and beauty, so take your time and enjoy the process of bringing your creations to life with a perfect glaze.



- 15 Easy RV Remodel Ideas on a Budget - April 13, 2025
- 15 Modern Balcony Railing Designs for Sleek Outdoor Spaces - April 12, 2025
- 35 Easiest Camping Meals to Make Ahead & Keep Everyone Full - March 31, 2025